Umbrella Meshes: Volumetric Elastic Mechanisms for Freeform Shape Deployment
Yingying Ren, Uday Kusupati, Julian Panetta, Florin Isvoranu, Davide Pellis, Tian Chen, Mark Pauly
View presentation:2022-10-19T16:45:00ZGMT-0600Change your timezone on the schedule page
2022-10-19T16:45:00Z
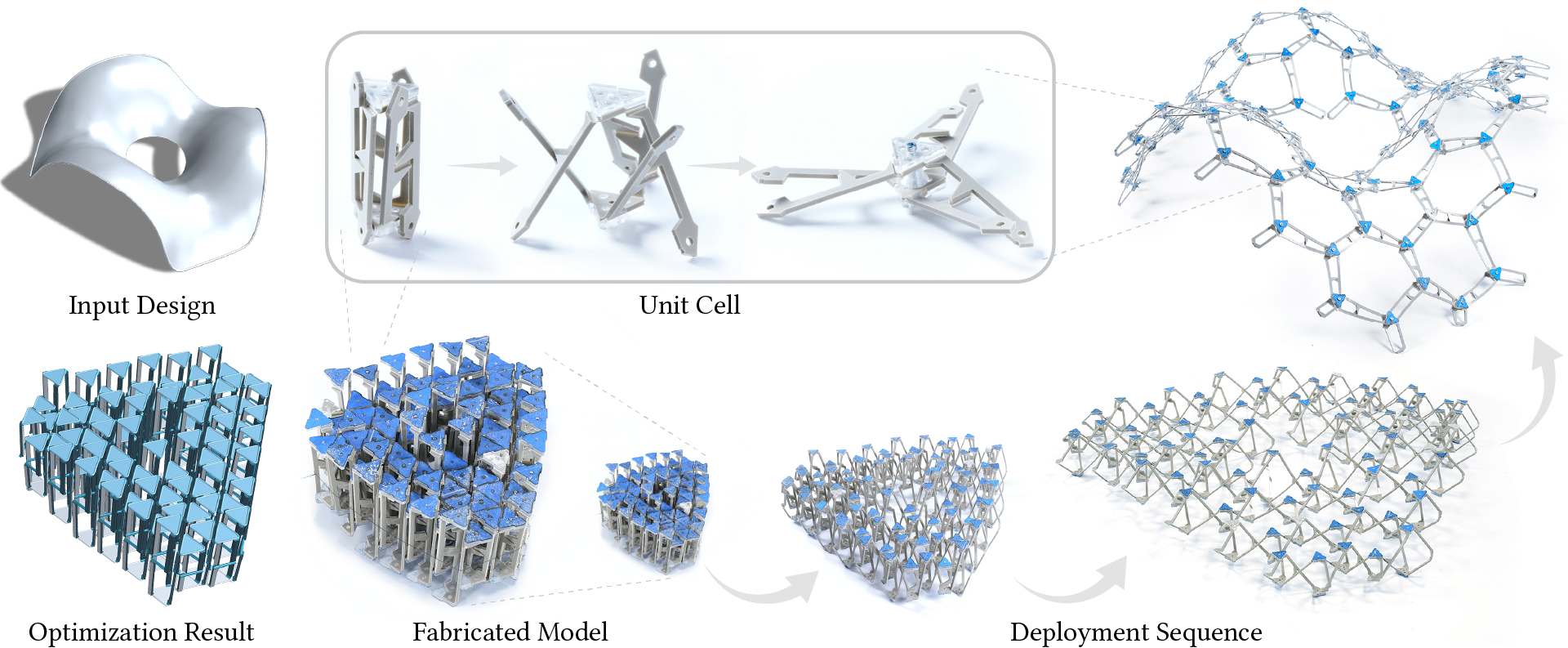
Prerecorded Talk
The live footage of the talk, including the Q&A, can be viewed on the session page, SIGGRAPH Invited Talks.
Fast forward
Keywords
Deployable structure, physics-based simulation, numerical optimization, computational design, fabrication
Abstract
We present a computational inverse design framework for a new class of volumetric deployable structures that have compact rest states and deploy into bending-active 3D target surfaces. Umbrella meshes consist of elastic beams, rigid plates, and hinge joints that can be directly printed or assembled in a zero-energy fabrication state. During deployment, as the elastic beams of varying heights rotate from vertical to horizontal configurations, the entire structure transforms from a compact block into a target curved surface. Umbrella Meshes encode both intrinsic and extrinsic curvature of the target surface and in principle are free from the area expansion ratio bounds of past auxetic material systems. We build a reduced physics-based simulation framework to accurately and efficiently model the complex interaction between the elastically deforming components. To determine the mesh topology and optimal shape parameters for approximating a given target surface, we propose an inverse design optimization algorithm initialized with conformal flattening. Our algorithm minimizes the structure's strain energy in its deployed state and optimizes actuation forces so that the final deployed structure is in stable equilibrium close to the desired surface with few or no external constraints. We validate our approach by fabricating a series of physical models at various scales using different manufacturing techniques.